
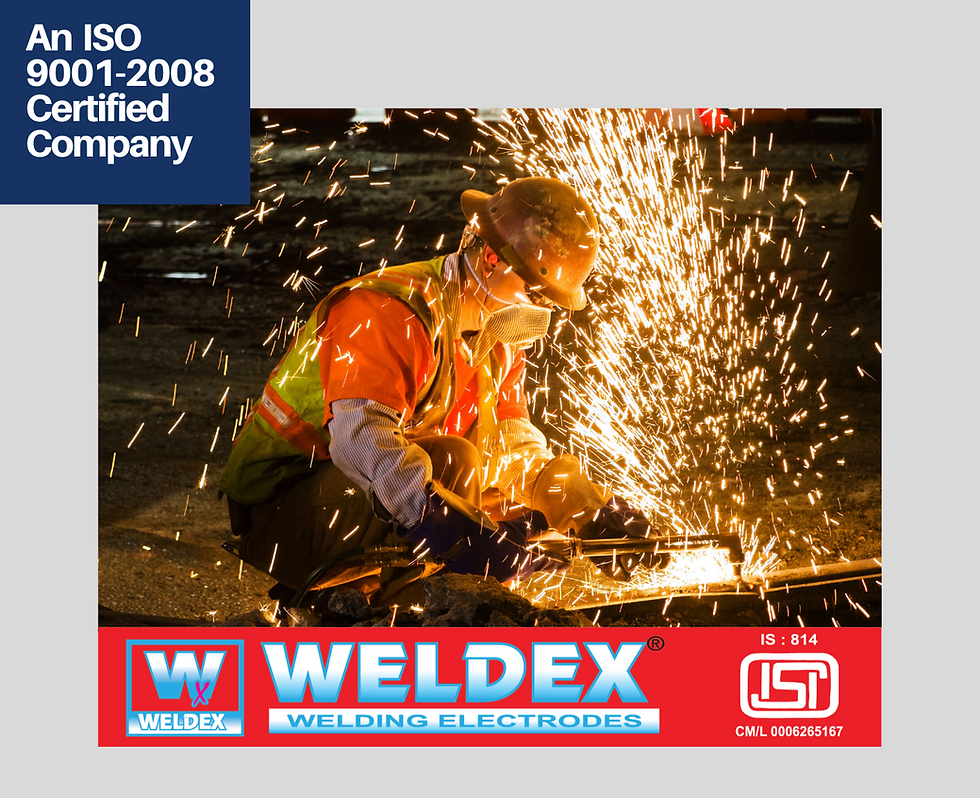.png)
Weldex
Classification
IS 814 1991 : ER 4211
Identification
Name Printed – Mangalum 6013
Current Condition – D [+] A50
Approved and Certified by
Bureau of Indian Standards
As per IS : 814 - CM/L 006265167
Applications
The wide range of applications in mild steel
includes Ship Hulls, Storage Tanks, Rail
Wagons and Coaches, Bridges, Machinery
Construction, Buildings, Auto Parts.
Characteristics
WELDEX is a medium coated all
position rutile electrode. It is suitable for light and medium structural works.
The weld deposit is consistent in
mechanical and radiographic quality.
Several pleasing features in its welding
performances are
- Ease of manipulation in all position
- Stable and smooth arc
- Low spatter
- Easily detachable slag
- Smooth, well rippled shining beads
Technical Details
Current Conditions (AMPS)
2.50 mm
50-80
3.15 mm
80-130
4.00 mm
115-165
5.00 mm
170-210
Weld Metal Chemistry (%)
C
0.05-0.07
Mn
0.35-0.50
Si
0.3 max
S
0.03 max
P
0.03 max
All Weld Mechanical Properties
Ultimate
tensile
strength
N/mm2
Yield
strength
N/mm2
Elongation
5.65 SO%
Impact
in joules
at 0C
480-560
380-480
22 min
47 min
Packing
Size (mm)
2.50 x 350 mm
3.15 x 350 mm
4.00 x 450 mm
5.00 x 450 mm
No. of electrodes/carton
125
90
60
40
No. of electrodes/box
1500
1080
720
480
Weldex Cutting Rod
Characteristics and applications
-
High arc force for deep penetration and cutting action.
-
Ideal for piercing and cutting all metals by the electric arc process and for removing runners and risers in foundry.
-
The electrodes strikes are easily and achieves clean cuts even on thicker materials.
-
The arc force is excellent and operates at high currents without getting over heated.
Instructions : Set up the work piece so that molten metal can run off easily. It is advisable to execute an up and down sawing movement, pushing the molten metal away with the electrode.
Weldex Electrodes - 7018
IS-EB - 5426 H3JX
AWS : E - 7018
-
An extra low hydrogen, radiographic quality, medium heavy coated, iron powder type electrode that is highly resistant to hydrogen - induced embrittlement.
-
Specially recommended for high strength welds on mild steels, medium carbon and low alloy high strength steels.
-
Deposition efficiency 115%.
-
Used on a variety of steels providing unique hydrogen-free deposits with superior impact resistance at normal and sub-zero temperatures.
-
Recommended applications include critical pressure vessels, high-pressure piping, blast furnace steel work, heavy welded fabrication as replacement for castings, pen-stocks, bridges, atomic reactor shell, overhead cranes, steel gears,loco frames, etc.
C
0.075
Mn
1.00
Si
0.45
S
0.030
P
0.030
[ APPROVED BY : I.B.R ]
Weldex-650
Characteristics and applications
-
A medium coated air-hardening type of electrode for hardfacing on mild steel,carbon and allow steel with hardness of 600 BHN approx.
-
Suitable for machine parts subjected to abrasive wear.
-
For surfacing/rebuilding of crusher hammers, cane cutting knives, conveyor buckets, drilling bits, shears and croppers, oil expellers, mine rails, caterpillar treads,mixer blades, dipper teeth, etc.
Instructions : Keep electrode dry. Use short arc and low welding speed. Employ short stringer beads. A buffer layer of EKNOWELD-7018 on carbon steels and EKNOWELD-18/8/6(S) on stainless steel, is necessary for austenitic managanese steel. Deposit can
only be ground finished. Deposit not more than 2 layers.
Mechanical properties of all weld metal
Hardness : 500-600 BHN (on 2 layer deposit)
C
0.40-0.70
Mn
0.20-0.40
Si
0.30-0.50
Cr
6.00-7.50
Weldex - SS Electrodes- 308
-
An all positional radiographic quality low carbon 19/10 stainless steel electrode with controlled ferrite content [3-7%] maximum resistance to corrosion and cracking.
-
High arc stability and low spatter losses and weld metal has excellent creep strength.
-
Resistant to inter-crystalline corrosion and suitable for welding ferrite steels of 13 to 17% chromium type. resistant to scaling up to 800°C.
-
For welding of AISI type : 301, 302, 304 and 308, German steel nos. 4016, 4501, 4300,4301, for building up surfaces of pump impellers, shafts, chemical plants.